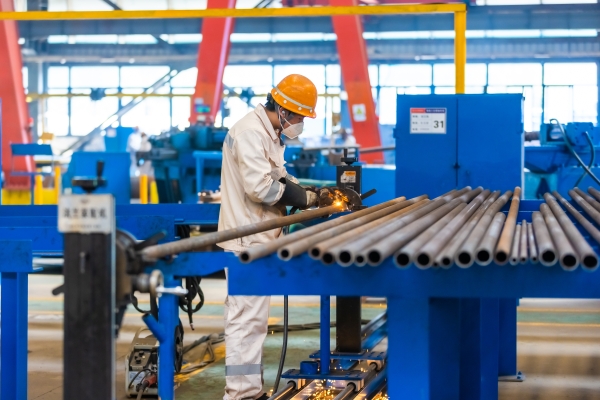
3月25日,舟山中远海运重工管加车间内呈现出一派繁忙而有序的景象。几名工人熟练地操控着崭新的小直管流水线,管材在传送带上有序移动,装配、焊接、打磨工序无缝衔接,一气呵成。相较于以往,如今同样工作时间,流水线的产出量实现翻倍,人均单日产能从原本不足50根跃升至100根以上,生产效率得到了显著提升。
这条高效的流水线,是制造工区近期通过自主设计研发和自行制作打造的小直管装、焊、磨一体化流水线。该流水线的投入使用,不仅使生产效率翻倍,还大幅降低了工人的劳动强度,这一创新成果的落地正悄然改变着车间的生产面貌。 过去,小直管制造长期依赖手工装配、人工蹲位焊接与打磨。这种模式下,效率较低,且工人劳动强度大,单日人均产能不足五十根。为提高生产效率,制造工区聚焦装、焊、磨三个核心环节,自主研发装配机、改造焊接变位机、优化材料托架,构建了小直管全流程一体化生产线。 装配工位“智能化升级”。自主研发的小直管装配机,采用固定托架与升降滑台设计,配合分度盘角度调节功能。这一创新设计消除人工校正环节,装配效率从单日50根提升至100根,耗时缩短50%。车间主管方磊介绍:“定位销与卡盘设计,让装配精度达到毫米级,为后续焊接奠定质量基础。” 焊接工位“全自动突破”。通过加装变位机、压紧气缸和可调接地装置,实现法兰内外口二氧焊自动变位焊接。单工位焊接效率提升70%,日均产能突破100根,且焊缝质量达到标准。 打磨工位“站立式革命”。将操作台高度提升至900mm,并设计滑轨式卸料通道,工人从蹲姿转为站立作业。单日打磨量从80根提升至100根,效率提升25%。现场操作人员反馈:“现在干活腰不酸了,管子打磨完直接滑走,省时又省力。” 在生产效率提升的同时,车间还通过材料循环利用、设备共享改造等措施,大幅降低生产成本;通过建立全流程检测体系,提升关键工序合格率。 面对管件设计数据与设备适配性挑战,工区还启动“双线攻坚计划”,一方面积极引进弯管机满足管子先焊后弯工艺,提高弯管精度和效率;另一方面,优化关键设计参数,实现设计与生产无缝对接,提升管件与设备的适配率。同时,工区持续优化小直管流水线生产流程,全力打造“智能排产-自动生产-实时质检”闭环体系,助力企业高质量发展。(方磊、乐帅、匡倩/文 夏赵丹/摄) |