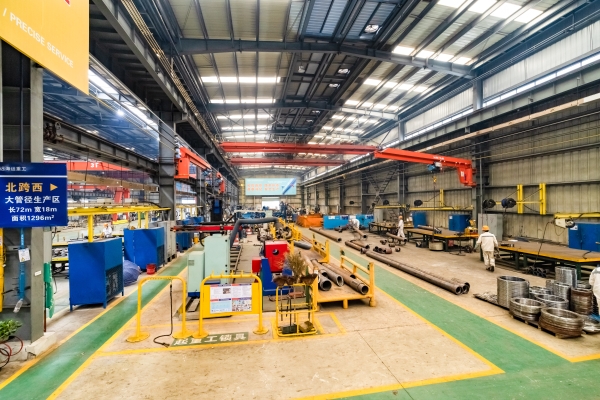
在当前激烈竞争的市场环境下,企业的持续发展需要不断地创新与变革。舟山中远海运重工积极响应时代需求,持之以恒深学川崎,结合企业实际生产,对标先进做法,大力推行精益管理,持续提升企业核心竞争力。 管加车间作为企业制造生产体系中的重要组成部分,深入剖析生产流程,全力推进管加车间大管生产流程再造优化工作。经过四个月的不懈努力与全面推行,如今管加车间的大管生产线呈现全新的面貌,阶段性成效显著,在生产流程、生产效率以及生产质量等方面均实现了大幅提升。 在生产方式优化方面,实现了全面革新。过去,大管生产线管子制作方式单一,下料后直接进行整体装配和焊接,整个过程完全依赖工人手动操作。特别是对工艺要求颇高的管件,对工人焊接技术的考验更为严苛,而大部分大管件都需借助吊运装置翻面焊接,焊接接头多,不仅使得焊工劳动强度增大,难以长时间连续作业,而且焊缝焊接稳定性也存在一定欠缺。 而现在,管加车间结合精益管理理念,对生产方式进行了彻底变革,所有管件采用小组立拆分焊接后再总组制作的方式,支管和弯头进行二次装配,彻底改变了传统的整根制作与焊接模式。通过优化减少不必要的动作和时间浪费,大幅提高生产效率。 在设备布局上,根据生产流程的先后顺序和物料流动方向,对工位和焊接设备进行了科学合理地重新布置。车间还自制和购置了部分小设备,使各部件能够在管件焊接流水线、卡盘变位机、变位滚轮架、压紧式变位机上顺畅地进行作业,并巧妙地使用焊接摆动器配合焊接。这种布局不仅提高了设备的利用率,还减少了物料搬运的距离和时间,降低了生产成本。 同时,管加车间引入精益管理中的标准化作业理念,对焊接工艺和操作流程进行了标准化制定。明确了每个工序的操作规范、质量标准和时间要求,使得普通人员经简单培训后即可按照标准操作,有效降低了对焊工技能的依赖,缓解了用工压力,拓宽了人力资源渠道。 在生产效率提升方面也取得了显著成效。以DN300法兰焊接为例,人工焊接原本需要42分钟,而采用设备焊接后仅需30分钟,每道焊缝节约12分钟。以63.6k项目的445根大管为例,平均每根管有二道缝,按照总DN242664计算,共节约时间162小时。仅这一项,就节约了成本12960元。 除了直接的时间和成本节约,流程再造还带来了诸多潜在效益。通过优化管理,合理安排生产计划,根据实际需求进行生产和配送,有效减少了库存积压和浪费,进一步降低了生产成本。同时,报检时间的缩短更加快了整体生产进度,为产品交付提供了有力保障,从而为客户带来了更优质的品质和更快捷的服务体验。 在流程再造过程中,注重员工培训与技能提升,定期组织员工学习精益管理知识和先进的焊接技术,培养员工精益思维和创新意识,提高员工的协作能力,为生产流程的顺畅运行和持续优化提供了坚实的人才支撑。 管加车间通过持之以恒深学川崎、对标先进,积极融入精益管理的做法,在大管生产线流程再造优化方面不仅提升了生产工序能力,更为企业的高质量持续发展注入了新动力。(潘小文、方磊/文 夏赵丹、张馨月/摄) |